CNC turning – profile roughing
In this learning path we will learn about roughning operation on CNC turning machine.
First step in CNC machining is analysing desired final product and determining proper order of neccesary steps and operations which must be taken to achieve desired result. By looking at this picture try to make a list of operations needed to get to desired shape of final product.
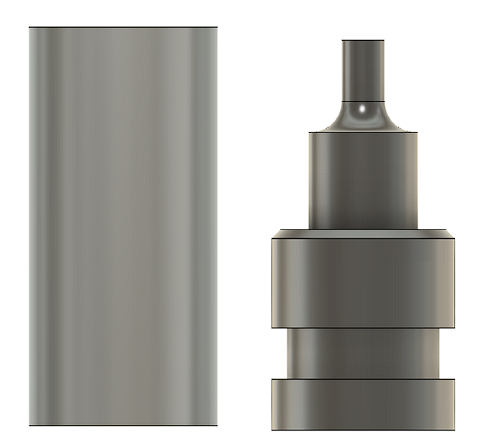
Read the text explaining the process of profile roughning for CNC turning.
Profile roughing in CNC turning is a machining process used to remove excess material from a workpiece to create the desired shape or profile. The process can be divided into several key phases:
- Workpiece Setup: The process begins with securing the workpiece firmly in the chuck of the CNC lathe. The workpiece is typically made of metal or plastic and is often cylindrical in shape.
- Tool Selection: A cutting tool suitable for roughing operations is selected. This tool is usually a carbide insert or solid carbide tool with multiple cutting edges designed to efficiently remove material.
- Tool Path Programming: The CNC programmer creates a toolpath using CAM (Computer-Aided Manufacturing) software. The toolpath defines the path that the cutting tool will follow as it removes material from the workpiece. In profile roughing, the toolpath typically follows the contour of the desired profile while removing material to a certain depth.
- Setting Cutting Parameters: The CNC operator sets the cutting parameters such as cutting speed, feed rate, and depth of cut based on the material of the workpiece, tooling, and desired surface finish. In roughing operations, higher cutting speeds and feed rates are often used to maximize material removal rates.
- Execution: The CNC machine is programmed with the toolpath and cutting parameters. The machine then automatically moves the cutting tool along the programmed path, gradually removing material from the workpiece. The cutting tool may traverse back and forth along the profile, removing material in layers or passes until the desired depth or shape is achieved.
- Chip Evacuation: As material is removed, chips are generated. Proper chip evacuation is essential to prevent chip buildup, tool wear, and surface finish issues. This is often achieved using coolant or cutting fluid to lubricate the cutting process and aid in chip removal.
- Monitoring and Inspection: Throughout the machining process, operators may monitor the operation to ensure that everything is running smoothly. Periodic inspections of the workpiece may also be conducted to verify dimensional accuracy and surface finish.
- Completion: Once the roughing operation is complete, the workpiece may undergo additional machining processes such as finishing or fine-tuning to achieve the final desired dimensions and surface quality.
Analyse the video and answer following questions:
1. Have you noticed any errors in roughning operation? What are they?
2. Has the operation achieved shape of final product?
3. What other operations are requirde to finalise product?
4. What changes would you suggest to improve roughning operation?
Resource information