CNC – Introduction to CNC lathe
First steps into uderstanding of CNC lathe
CNC turning, also known as computer numerical control turning, is a machining process used to create cylindrical parts by removing material from a rotating workpiece. It is one of the most common and versatile machining operations in manufacturing.
In CNC turning, a lathe machine is used to hold and rotate the workpiece while a cutting tool removes material to achieve the desired shape. The cutting tool is controlled by a computer program, which provides precise instructions for tool movement and material removal.
The process begins by mounting the workpiece on the lathe’s spindle. The spindle rotates the workpiece at a high speed while the cutting tool, positioned parallel to the spindle axis, moves along the workpiece to remove material. The cutting tool may be stationary, or it can move in multiple axes to create complex shapes and features.
The process begins by mounting the workpiece on the lathe’s spindle. The spindle rotates the workpiece at a high speed while the cutting tool, positioned parallel to the spindle axis, moves along the workpiece to remove material. The cutting tool may be stationary, or it can move in multiple axes to create complex shapes and features.
CNC turning offers several advantages over conventional manual turning. It allows for higher precision, repeatability, and efficiency in producing parts. The computer control enables intricate and complex designs to be accurately replicated. Additionally, CNC turning machines can often perform multiple operations in a single setup, reducing the need for manual intervention and increasing productivity.
This process is commonly used to produce parts such as shafts, rods, bushings, pulleys, and other cylindrical components. The materials that can be used for CNC turning include metals like steel, aluminum, brass, and titanium, as well as plastics and various composites.
Overall, CNC turning is a fundamental machining process that plays a vital role in many industries, including automotive, aerospace, medical device manufacturing, and general engineering.
Determine which are starting and final dimensions of this workpiece.
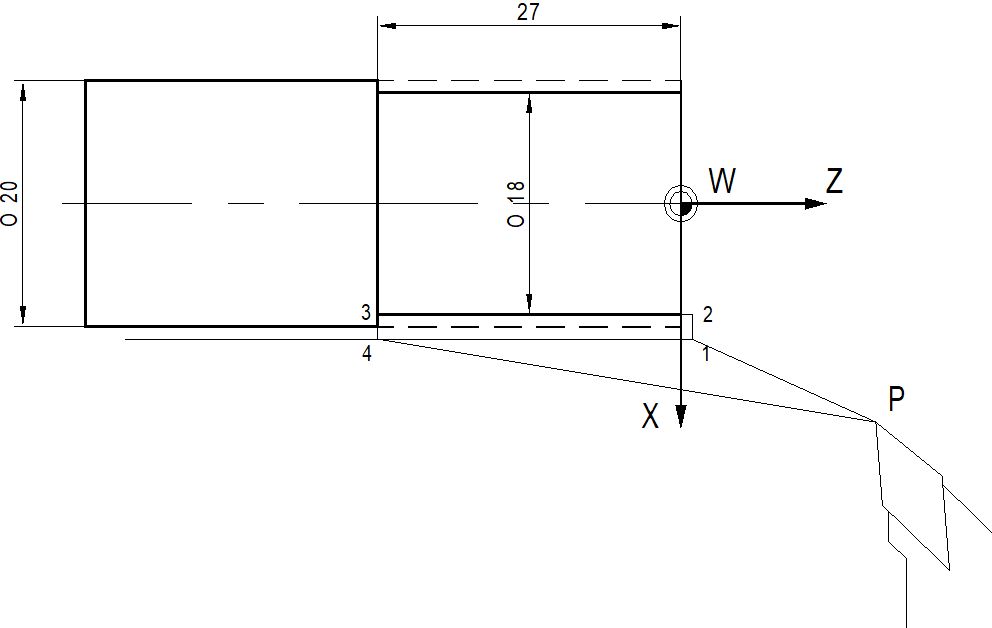
Whatch the video about removing material using CNC turning machine
Since CNC machine can’t do anything without operator telling it to do so, one of the most important tasks is correctly programming the path of the cutting tool without causing collision with other machine parts or ramming the tool into workpiece at wrong place/wrong speed.
In CNC machining, a coordinate system is used to define the positions and movements of the cutting tool and the workpiece. It provides a reference framework that enables precise control of tool paths and material removal.
The coordinate system in CNC machining is typically a Cartesian coordinate system, similar to the X, Y, and Z axes used in mathematics and physics. However, in CNC machining, an additional rotational axis, often called the A-axis or C-axis, may be added for multi-axis machines.
Here's a breakdown of the coordinate system in CNC machining:
X-axis: The X-axis represents the horizontal movement of the cutting tool or the workpiece along its length. Positive values move the tool or workpiece to the right, and negative values move it to the left.
Y-axis: The Y-axis represents the vertical movement of the cutting tool or the workpiece perpendicular to the X-axis. Positive values move the tool or workpiece upward, and negative values move it downward.
Z-axis: The Z-axis represents the depth or axial movement of the cutting tool into the workpiece. Positive values move the tool downward into the workpiece, and negative values move it upward, away from the workpiece.
A-axis or C-axis: In multi-axis machines, an additional rotational axis may be present. The A-axis or C-axis allows the workpiece or cutting tool to rotate around a specific axis. This rotational movement enables the machining of complex geometries and features.

These axes form the foundation of the coordinate system in CNC machining. Each axis has a corresponding axis motor that moves the cutting tool or the workpiece with high precision based on the instructions provided by the CNC program.
To specify a position in the coordinate system, the distances or displacements along each axis are typically given as absolute or relative values in units such as millimeters or inches. These values determine the tool’s or workpiece’s position in relation to the machine’s reference point, known as the machine origin or work coordinate system (WCS).
The CNC programmer defines the WCS based on the part design and manufacturing requirements. By specifying coordinates in the CNC program, the cutting tool can be accurately positioned and moved along the desired tool paths to shape the workpiece as intended.
In summary, the coordinate system in CNC machining provides a framework for precise positioning and movement control along the X, Y, Z, and potentially additional rotational axes. It allows for accurate machining operations and the creation of complex geometries with high precision.
Solve the learning app
Using the picture from activity 2, fill in correct values for coordinates of 4 points used for programming the path of cutting tool.
Resource information